Laser Assembly System: Sale-Service-Support
There is one machine for sale.
If you have one or more of these unique Laser Assembly Systems and need service and support for you machine, Ray Prasad can arrange it from former BeamWorks Engineers who designed and built those machines.
Spark 400 is a total assembly system. It is the TOTAL SMT line for many companies if their volume is low. However, when it comes to high volume repair, there is nothing like Spark 400 on this planet. None. Here is a brief Description of the machine.
BeamWorks Spark 400 Laser Assembly System:
BeamWorks Spark 400 Laser Assembly System, unlike hot air repair systems, heats only the component to be removed or replaced without affecting the neighboring components.
How is it possible? With miniaturization of electronics products like iPad and iPhone, the spacing between components is practically zero. boards. Because the laser beam is very narrow, components even 0.020" (20 mil) away do not experience any heat.
Compare that to minimum 150 mils for hot air repair systems. Laser systems heat the package without melting the solder joints of neighboring components while keeping the board cool enough to touch. With hot air systems, melting solder joints of neighboring components is a serious concern. Using correct hot air nozzles and shielding adjacent components can minimize this problem.
However, hot air nozzles are needed for each type and size of component assuming you have the space between components. This adds to the cost and complexity of repair. Laser systems are also perfect for soldering backward compatibility assemblies (almost the entire board is tin-lead but the BGAs are lead free) commonly encountered in high end military and other applications.
Automated Rework Systems
If you do deal with high-volume rework, you are in big trouble with existing technology because it takes more than 10 minutes to remove and replace one component. That is only five to six components per hour. For 100,000 components, that is 10 years! This is when you need an automated rework system.
To automate rework fully, not a single machine but an assembly system that can selectively dispense solder paste, place components and reflow components without heating neighboring components is needed. The system also needs to be fairly fast to assemble quickly and automatically to meet the mass rework requirements.
To provide a real relief, it must be able to selectively assemble many part types without the problem (and the cost that can add up quickly) of changing nozzles and stencils for each part type. The automated rework system needs to perform all the functions of a rework operation — component removal, solder paste dispensing, component placement and selective soldering. If the machine can dispense paste (or flux as generally is the case because enough solder is left on the pad after component removal), there is no need to spend money on ministencils for each component.
Paste or flux dispensing should be done either as dots or a thin strip of paste or flux. To prevent melting of solder joints of adjacent components, the heat source needs to be laser, possibly diode laser.
Important benefits of a diode laser are that it does not reflow solder joints of adjacent components even if they are only 0.020" away and does not need any nozzles. Also, if the heat source for reflow is a diode laser, the moisture-sensitive components already assembled (or to be assembled) do not require baking. This is very important when you want to selectively assemble only certain components.
Streamline Your Rework Processes
Because all operations are performed without human intervention, quality is consistent even when you are repairing thousands of boards.
Because reflow time will be in milliseconds as opposed to minutes as in conventional systems, the intermetallic thickness would be less than a micron (compared to 5 mm in conventional processes).
Thin intermetallic and complete independence from human variables improve solder joint quality — one key rework concern.
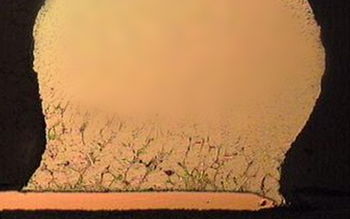
Registration is Open for SMT Course
Ray Prasad will be teaching his flagship SMT course: