Building SMT Assemblies with Missing Components to Improve Quality and Delivery
From the title of this column, you might find it strange that someone with a reasonable understanding of the SMT industry would even suggest that quality and delivery could improve by building assemblies with missing components. Of course, it is always better to have all components on hand before assembly but there are times when this is not the case and one must deal with missing component issues. For a change, this column is not about materials and process technology but about production planning and scheduling issues as they relate to missing components. This month’s column will discuss how to reduce cycle time and improve quality by building assemblies even with missing components. This unusual recommendation is based on a recently available innovative assembly system.
In our industry there are two key manufacturing concerns ¾ quality and delivery. This is especially true in contract manufacturing (CM). Problems arise either because the product is late or there is some complaint about product quality. Sometimes there are complaints about both quality and delivery.
There are many reasons for quality and delivery problems. It depends on whether you are the OEM or the subcontractor. In an OEM’s view, the quality and delivery problems primarily are because of poor process control and production planning by the subcontractor.
On the other hand, if you are the subcontractor, it really is not your fault. The quality problems are because of the poor design for manufacturing (DFM) used by the OEM. And the reason the subcontractor has a hard time delivering products on time is because of repeated engineering change notices (ECN) and poor product volume forecasting by the OEM. This makes it difficult to order enough parts in time without incurring excessive inventory carrying cost. And being restricted to buying parts, especially long lead parts, only from suppliers approved by the OEM only compounds the problem.
In my consulting practice, I find that both the OEMs and the subcontractors are partially right and the truth lies somewhere in between. However, a main reason for delivery problems is component availability before assembly. Very often there are missing components before assembly.
Note that quality and delivery problems are not unique to subcontractors. OEMs building in-house boards face the same problems. So, as the production manager responsible for shipping the product, whether an OEM or a subcontractor, what options are available if components are missing? Should boards be partially assembled or should assembly wait until all components arrive?
Waiting is a gamble because it is unknown when those missing components will arrive. Instead, maybe the production manager will partially build the assemblies with missing parts and then hand solder them when the missing components arrive. But this option does not provide relief either because hand soldering will not only increase cost but also will reduce product quality. So, as a production manager, there really is not a good option to keep customers satisfied.
Of course, it would be better if all the components were available and no one had to deal with missing components. But let’s be realistic. As the people on the front line responsible for manufacturing know, no matter how perfect production planning and component ordering systems, there are times when components will not arrive as scheduled. This is when the lack of options comes into play. That is, until now. This brings me back to where I started ¾ how to build assemblies with missing components while reducing cycle time and improving quality.
The key reason to wait for all components before proceeding with the assembly is the need to print solder paste for all components and solder them simultaneously in the convection reflow oven. If components, which happen to be fine-pitch components with high pin counts in a high-volume line, were missing, numerous skilled operators would be needed to meet the production demand. Even then, rework would be high, compounding quality and delivery problems.
Addressing Industry Concern
What is needed is an automated selective assembly system (not a single machine but an assembly system) that can selectively dispense solder paste, place components and reflow solder the missing components without impacting already assembled components. The system also must automatically assemble and be fairly fast to meet the needs of a high-volume line. Additionally, it must selectively assemble many part types because typically there are many components missing. Such a machine to selectively assemble surface mount components did not exist. That is, until last month.
Those who attended APEX last month probably saw the automated selective assembly system ¾ Spark 400 by BeamWorks. Before I briefly describe this machine, let me make a public disclosure to avoid any conflict of interest. I have significant interest in BeamWorks. I have been working with the company since its inception about three years ago and currently play a major role in its operation.
Spark 400 from BeamWorks is an automated selective assembly system that performs all functions of a typical SMT line ¾ solder paste dispensing, component placement, laser soldering and inspection. Soldering and inspection functions are performed concurrently to provide real-time feedback on solder joint quality. This is the only system I know that automatically stops soldering when desired solder joint quality is achieved. It tailors heat input to a specific component as well as to a specific lead. If a certain lead of a given component is connected to power or ground plane, the laser soldering time is longer for that lead than the adjacent lead not connected to a heat sink.
Because the machine dispenses paste, a partially assembled board does not pose any problems as it would if a stencil were used. It does not require separate programming for dispensing, placement and soldering. Paste dispensing is done either as dots (as would be the case for array packages) or a thin strip of paste (as would be the case for peripheral components). Then, using the same computer-aided design (CAD) data, it places components and quickly solders them using four diode lasers. What is really important is that the selective assembly of missing surface mount components does not affect in any way the components that already have been assembled on the conventional SMT line. Also, because the heat source for reflow is a diode laser, the moisture-sensitive components already assembled (or to be assembled) do not require baking. This is important to selectively assemble only certain components.
Having such a system makes production planning a lot easier for the production manager responsible for meeting delivery dates. For example, the production plan does not have to be reshuffled for the SMT line if some components do not make it on time because assembly can proceed with one or more missing components. Additionally, this machine makes the best use of the expensive equipment in the SMT line. Any time the line stops because of last minute changes in production scheduling, due to missing components, can be very expensive. Proper machine utilization is key to making money, especially in a very competitive industry with low profit margins.
The BeamWorks machine provides flexibility to the production manager. When those missing components arrive, they can be soldered off-line or in-line without impacting the current production plan. This will improve delivery because partially assembled boards with missing components can be assembled quickly and automatically. Additionally, the delivery dates of other products with or without missing components will be improved because they will not be affected by the chain reaction of missing components in one product impacting the delivery dates of other products.
Missing components have been one reason for quality and delivery problems in manufacturing. Using the selective automated assembly system from BeamWorks provides a cost-effective system for addressing this common industry problem.
SMT
RAY P. PRASAD is an SMT Editorial Advisory Board member and author of the textbook Surface Mount Technology: Principles and Practice. Additionally, he is president of BeamWorks Inc., a supplier of selective automated assembly systems, located in Portland, OR and founder of the Ray Prasad Consultancy Group, which specializes in helping companies establish strong internal SMT infrastructure. Contact him on his Web site: www.rayprasad.com.
In our industry there are two key manufacturing concerns ¾ quality and delivery. This is especially true in contract manufacturing (CM). Problems arise either because the product is late or there is some complaint about product quality. Sometimes there are complaints about both quality and delivery.
There are many reasons for quality and delivery problems. It depends on whether you are the OEM or the subcontractor. In an OEM’s view, the quality and delivery problems primarily are because of poor process control and production planning by the subcontractor.
On the other hand, if you are the subcontractor, it really is not your fault. The quality problems are because of the poor design for manufacturing (DFM) used by the OEM. And the reason the subcontractor has a hard time delivering products on time is because of repeated engineering change notices (ECN) and poor product volume forecasting by the OEM. This makes it difficult to order enough parts in time without incurring excessive inventory carrying cost. And being restricted to buying parts, especially long lead parts, only from suppliers approved by the OEM only compounds the problem.
In my consulting practice, I find that both the OEMs and the subcontractors are partially right and the truth lies somewhere in between. However, a main reason for delivery problems is component availability before assembly. Very often there are missing components before assembly.
Note that quality and delivery problems are not unique to subcontractors. OEMs building in-house boards face the same problems. So, as the production manager responsible for shipping the product, whether an OEM or a subcontractor, what options are available if components are missing? Should boards be partially assembled or should assembly wait until all components arrive?
Waiting is a gamble because it is unknown when those missing components will arrive. Instead, maybe the production manager will partially build the assemblies with missing parts and then hand solder them when the missing components arrive. But this option does not provide relief either because hand soldering will not only increase cost but also will reduce product quality. So, as a production manager, there really is not a good option to keep customers satisfied.
Of course, it would be better if all the components were available and no one had to deal with missing components. But let’s be realistic. As the people on the front line responsible for manufacturing know, no matter how perfect production planning and component ordering systems, there are times when components will not arrive as scheduled. This is when the lack of options comes into play. That is, until now. This brings me back to where I started ¾ how to build assemblies with missing components while reducing cycle time and improving quality.
The key reason to wait for all components before proceeding with the assembly is the need to print solder paste for all components and solder them simultaneously in the convection reflow oven. If components, which happen to be fine-pitch components with high pin counts in a high-volume line, were missing, numerous skilled operators would be needed to meet the production demand. Even then, rework would be high, compounding quality and delivery problems.
Addressing Industry Concern
What is needed is an automated selective assembly system (not a single machine but an assembly system) that can selectively dispense solder paste, place components and reflow solder the missing components without impacting already assembled components. The system also must automatically assemble and be fairly fast to meet the needs of a high-volume line. Additionally, it must selectively assemble many part types because typically there are many components missing. Such a machine to selectively assemble surface mount components did not exist. That is, until last month.
Those who attended APEX last month probably saw the automated selective assembly system ¾ Spark 400 by BeamWorks. Before I briefly describe this machine, let me make a public disclosure to avoid any conflict of interest. I have significant interest in BeamWorks. I have been working with the company since its inception about three years ago and currently play a major role in its operation.
Spark 400 from BeamWorks is an automated selective assembly system that performs all functions of a typical SMT line ¾ solder paste dispensing, component placement, laser soldering and inspection. Soldering and inspection functions are performed concurrently to provide real-time feedback on solder joint quality. This is the only system I know that automatically stops soldering when desired solder joint quality is achieved. It tailors heat input to a specific component as well as to a specific lead. If a certain lead of a given component is connected to power or ground plane, the laser soldering time is longer for that lead than the adjacent lead not connected to a heat sink.
Because the machine dispenses paste, a partially assembled board does not pose any problems as it would if a stencil were used. It does not require separate programming for dispensing, placement and soldering. Paste dispensing is done either as dots (as would be the case for array packages) or a thin strip of paste (as would be the case for peripheral components). Then, using the same computer-aided design (CAD) data, it places components and quickly solders them using four diode lasers. What is really important is that the selective assembly of missing surface mount components does not affect in any way the components that already have been assembled on the conventional SMT line. Also, because the heat source for reflow is a diode laser, the moisture-sensitive components already assembled (or to be assembled) do not require baking. This is important to selectively assemble only certain components.
Having such a system makes production planning a lot easier for the production manager responsible for meeting delivery dates. For example, the production plan does not have to be reshuffled for the SMT line if some components do not make it on time because assembly can proceed with one or more missing components. Additionally, this machine makes the best use of the expensive equipment in the SMT line. Any time the line stops because of last minute changes in production scheduling, due to missing components, can be very expensive. Proper machine utilization is key to making money, especially in a very competitive industry with low profit margins.
The BeamWorks machine provides flexibility to the production manager. When those missing components arrive, they can be soldered off-line or in-line without impacting the current production plan. This will improve delivery because partially assembled boards with missing components can be assembled quickly and automatically. Additionally, the delivery dates of other products with or without missing components will be improved because they will not be affected by the chain reaction of missing components in one product impacting the delivery dates of other products.
Missing components have been one reason for quality and delivery problems in manufacturing. Using the selective automated assembly system from BeamWorks provides a cost-effective system for addressing this common industry problem.
SMT
RAY P. PRASAD is an SMT Editorial Advisory Board member and author of the textbook Surface Mount Technology: Principles and Practice. Additionally, he is president of BeamWorks Inc., a supplier of selective automated assembly systems, located in Portland, OR and founder of the Ray Prasad Consultancy Group, which specializes in helping companies establish strong internal SMT infrastructure. Contact him on his Web site: www.rayprasad.com.
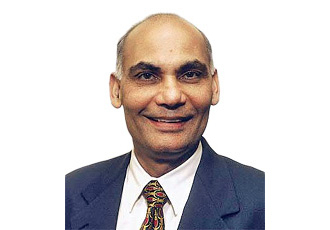
Registration is Open for SMT Course
Ray Prasad will be teaching his flagship SMT course: