SMT- Placing an AOI System in the SMT Line
There are various inspection and test methods used in the industry. The visual inspection method is the most common and inexpensive but is very operator dependent. The X-ray method is expensive, slow and has limited capability. The automated optical inspection (AOI) is faster but expensive. And in-circuit test (ICT) and functional tests sometimes also are used as inspection tools but they have limited capabilities. In this column, I will discuss visual and AOI methods. In my future columns, I will cover ICT, X-ray and laser inspection methods.
Visual Inspection
The most common and widely used method of inspection is visual inspection at 2 to 10X magnification using a magnifier or a microscope. J?STD?001 requires inspection at 2 to 4X for all devices with lead pitches greater than 0.020". Magnification of 10X is required for fine-pitch devices with lead pitches 0.020" and below. Higher magnification should be used for reference only.
The main problem with visual inspection is that it is operator-dependent and, hence, subjective. For example, if the same assembly is given to different inspectors, they will report different quality levels. A common response to this situation is to reduce the human factor and switch to one of many automated inspection systems.
AOI
As the industry has been moving toward finer pitches and ball grid arrays (BGA), visual inspection of solder joints has become either very difficult or impossible. Also, as previously discussed, even when feasible, visual inspection is very operator-dependent. As a result, the industry has been moving toward automated inspection systems. There are numerous systems on the market with wide range in prices. New machines are constantly introduced on the market.
In selecting the needed machine, you need to decide what you want the AOI system to do. For example do you want the machine to point out missing components, component polarity, placement accuracy, paste deposit or solder joint quality? It is important to keep in mind that most AOI machines do a decent job when it comes to identifying wrong polarity or missing components but may find it challenging to accurately identify solder joint quality.
No matter what type of equipment is used, general AOI system requirements should include accuracy, repeatability, speed, computer-aided design (CAD) compatibility, and false fails and false accepts (a very common problem when using the machine for solder joint quality inspection).
Sometimes, it is wrongly believed that automated inspection systems can be used for process control by changing the appropriate variables to correct defects on a real?time basis. For most systems, this may be wishful thinking at present because many of the changes necessary to prevent the problems require human intervention.
The only way to control solder joint quality on a real-time basis is if soldering and inspection systems are integrated. With such an integrated system, soldering joints either stops or continues depending on the individual solder joint heat input requirements. This simply is not possible in conventional reflow processes such as convection. Currently laser soldering systems with closed loop inspection features are commercially available to achieve such a goal.
However, there are no systems that really can pinpoint a given defect and identify its cause in all cases. Defect analysis may require human intervention and engineering judgment. For example, auto inspection systems largely depend on the mass and density of solder (insufficient, excess or none). Defects having more than one cause, however, could never be placed into only one of these three categories to meet the needs of an automated inspection system. Insufficient solder can be caused by voids, insufficient fillet or insufficient solder paste. The corrective actions for these defects are different, calling for human judgment and intervention.
Inspection Philosophies
There are two philosophies for inspection: Prevention or detection of defects. The appropriate approach should be prevention of defects because the focus is on process control and eliminating defects by implementing corrective action. In such an approach, AOI machines are placed either after the solder paste printer or after component placement (before reflow) in the SMT line.
Those who use the detection philosophy for inspection place the inspection machine at the very end of the SMT line — after the reflow oven. It is the last step in the manufacturing process to ensure that no bad product will escape from the factory.
Philosophically speaking, many would disagree with preventive methods of inspection. If you agree with this philosophy, where in the line should you place the AOI system?
The first option is to place the AOI systems right after paste printing. Since most defects are related to paste volume and print quality, this is a good place for the AOI system. What should such a system monitor? Only X-Y dimensions of paste including misprint or paste volume (X-Y-Z)? Paste volume measurement would be slower than X-Y measurement but would provide more useful data. This is more critical in some applications than others. For example, for ceramic array packages, paste volume is very critical to achieve desired solder joint quality.
The second option is to place the AOI system directly after the chip shooter. Here, misplaced or wrong small components including resistors and capacitors may be inspected for, as well as paste quality and volumes for BGAs and fine-pitch components, which are placed by different placement machines after chip shooters in the line. With their vision capability, they generally have better accuracy for larger packages.
The third option is to place the AOI system after the fine-pitch and BGA placement machine (and before reflow) to inspect for misplaced fine-pitch, BGAs and other large components. This is a good location because most defects are related to fine-pitch components. These are the options for believers of prevention philosophy.
If you are focusing on the detection method, you have the fourth option — to place the AOI system after reflow and look for poor solder joint quality. This is a good approach for companies with low defects that want to be sure unacceptable solder joints are caught before shipping to the end customer.
The fifth option is to incorporate both prevention and detection philosophies and place AOI systems after every process step — paste printing, the chip shooter, BGA and fine-pitch placement, and reflow. This option, certainly while making the day of the AOI salesman, may not be an affordable option.
Most people have limited budgets and must decide where in the SMT line to place the system. If buying only one AOI system, you may want to place it directly after the chip shooter where you can inspect for two major problems — misplacement or wrong component placement of smaller components and paste quality and volume for BGAs and fine-pitch components. Also, this happens to be the most critical location in determining overall quality.
Conclusion
Solder joint inspection is an after?the?fact step. A more effective practice is to take preventive action. That is, to implement process control to ensure that the problem does not occur. Does this mean that inspection is not necessary? Far from it. Inspection will have to continue to complete the loop on defect collection, to monitor the process and to implement corrective action so that the problem does not recur.
SMT
RAY P. PRASAD is an SMT Editorial Advisory Board member and author of the textbook Surface Mount Technology: Principles and Practice. Additionally, he is president of BeamWorks Inc. (www.beamworks.com), a supplier of selective automated assembly systems, located in Portland, OR and founder of the Ray Prasad Consultancy Group, which specializes in helping companies establish strong internal SMT infrastructure. Contact him from his Web site: www.rayprasad.com.
Visual Inspection
The most common and widely used method of inspection is visual inspection at 2 to 10X magnification using a magnifier or a microscope. J?STD?001 requires inspection at 2 to 4X for all devices with lead pitches greater than 0.020". Magnification of 10X is required for fine-pitch devices with lead pitches 0.020" and below. Higher magnification should be used for reference only.
The main problem with visual inspection is that it is operator-dependent and, hence, subjective. For example, if the same assembly is given to different inspectors, they will report different quality levels. A common response to this situation is to reduce the human factor and switch to one of many automated inspection systems.
AOI
As the industry has been moving toward finer pitches and ball grid arrays (BGA), visual inspection of solder joints has become either very difficult or impossible. Also, as previously discussed, even when feasible, visual inspection is very operator-dependent. As a result, the industry has been moving toward automated inspection systems. There are numerous systems on the market with wide range in prices. New machines are constantly introduced on the market.
In selecting the needed machine, you need to decide what you want the AOI system to do. For example do you want the machine to point out missing components, component polarity, placement accuracy, paste deposit or solder joint quality? It is important to keep in mind that most AOI machines do a decent job when it comes to identifying wrong polarity or missing components but may find it challenging to accurately identify solder joint quality.
No matter what type of equipment is used, general AOI system requirements should include accuracy, repeatability, speed, computer-aided design (CAD) compatibility, and false fails and false accepts (a very common problem when using the machine for solder joint quality inspection).
Sometimes, it is wrongly believed that automated inspection systems can be used for process control by changing the appropriate variables to correct defects on a real?time basis. For most systems, this may be wishful thinking at present because many of the changes necessary to prevent the problems require human intervention.
The only way to control solder joint quality on a real-time basis is if soldering and inspection systems are integrated. With such an integrated system, soldering joints either stops or continues depending on the individual solder joint heat input requirements. This simply is not possible in conventional reflow processes such as convection. Currently laser soldering systems with closed loop inspection features are commercially available to achieve such a goal.
However, there are no systems that really can pinpoint a given defect and identify its cause in all cases. Defect analysis may require human intervention and engineering judgment. For example, auto inspection systems largely depend on the mass and density of solder (insufficient, excess or none). Defects having more than one cause, however, could never be placed into only one of these three categories to meet the needs of an automated inspection system. Insufficient solder can be caused by voids, insufficient fillet or insufficient solder paste. The corrective actions for these defects are different, calling for human judgment and intervention.
Inspection Philosophies
There are two philosophies for inspection: Prevention or detection of defects. The appropriate approach should be prevention of defects because the focus is on process control and eliminating defects by implementing corrective action. In such an approach, AOI machines are placed either after the solder paste printer or after component placement (before reflow) in the SMT line.
Those who use the detection philosophy for inspection place the inspection machine at the very end of the SMT line — after the reflow oven. It is the last step in the manufacturing process to ensure that no bad product will escape from the factory.
Philosophically speaking, many would disagree with preventive methods of inspection. If you agree with this philosophy, where in the line should you place the AOI system?
The first option is to place the AOI systems right after paste printing. Since most defects are related to paste volume and print quality, this is a good place for the AOI system. What should such a system monitor? Only X-Y dimensions of paste including misprint or paste volume (X-Y-Z)? Paste volume measurement would be slower than X-Y measurement but would provide more useful data. This is more critical in some applications than others. For example, for ceramic array packages, paste volume is very critical to achieve desired solder joint quality.
The second option is to place the AOI system directly after the chip shooter. Here, misplaced or wrong small components including resistors and capacitors may be inspected for, as well as paste quality and volumes for BGAs and fine-pitch components, which are placed by different placement machines after chip shooters in the line. With their vision capability, they generally have better accuracy for larger packages.
The third option is to place the AOI system after the fine-pitch and BGA placement machine (and before reflow) to inspect for misplaced fine-pitch, BGAs and other large components. This is a good location because most defects are related to fine-pitch components. These are the options for believers of prevention philosophy.
If you are focusing on the detection method, you have the fourth option — to place the AOI system after reflow and look for poor solder joint quality. This is a good approach for companies with low defects that want to be sure unacceptable solder joints are caught before shipping to the end customer.
The fifth option is to incorporate both prevention and detection philosophies and place AOI systems after every process step — paste printing, the chip shooter, BGA and fine-pitch placement, and reflow. This option, certainly while making the day of the AOI salesman, may not be an affordable option.
Most people have limited budgets and must decide where in the SMT line to place the system. If buying only one AOI system, you may want to place it directly after the chip shooter where you can inspect for two major problems — misplacement or wrong component placement of smaller components and paste quality and volume for BGAs and fine-pitch components. Also, this happens to be the most critical location in determining overall quality.
Conclusion
Solder joint inspection is an after?the?fact step. A more effective practice is to take preventive action. That is, to implement process control to ensure that the problem does not occur. Does this mean that inspection is not necessary? Far from it. Inspection will have to continue to complete the loop on defect collection, to monitor the process and to implement corrective action so that the problem does not recur.
SMT
RAY P. PRASAD is an SMT Editorial Advisory Board member and author of the textbook Surface Mount Technology: Principles and Practice. Additionally, he is president of BeamWorks Inc. (www.beamworks.com), a supplier of selective automated assembly systems, located in Portland, OR and founder of the Ray Prasad Consultancy Group, which specializes in helping companies establish strong internal SMT infrastructure. Contact him from his Web site: www.rayprasad.com.
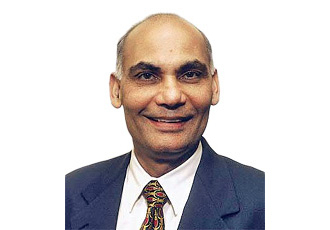
Registration is Open for SMT Course
Ray Prasad will be teaching his flagship SMT course: