SMT Solder Paste Printing For SMT Fine-pitch and Through-hole Components Part 2
Part 2 of a 2-part series.
In last month’s column (“Solder Paste Printing,” September 2000 SMT, p. 28-33), I discussed the basic process of solder paste printing, stencil types and design. In this column, I will apply those principles to fine-pitch and through-hole component paste printing on a mixed-assembly board.
Fine-pitch Paste Printing
When printing for fine pitch, it is important to control the smoothness and the dimensions of the stencil apertures, meaning laser-cut stencils should be considered. Fine pitch also requires different solder paste.
Solder paste print quality is very important because it accounts for numerous printed circuit assembly (PCA) defects. When using fine pitch, the problem is compounded, leading to bridging between adjacent leads.
Bridging is not the only common defect in fine-pitch printing. Inadequate paste deposition leads to insufficient solder or complete opens. In most companies, fine-pitch printing accounts for about half of all defects.
To avoid printing problems, some use dual?step stencils (0.005 to 0.006" for fine-pitch and 0.007 to 0.008" for other components). The stencil material, generally stainless steel, is etched down to a low thickness where the stencil aligns with fine-pitch component pads. Step stencils require a rubber squeegee to force the paste through the stencil holes. This is a good method for depositing the correct paste amount at specific locations (0.005 to 0.006" paste height for fine-pitch and 0.007 to 0.008" paste height for standard surface mount components).
A more recent method uses a metal squeegee and deposits the same paste thickness for both fine-pitch and other components. However, it is possible to deposit too much paste on the fine-pitch lands or too little paste on the standard surface mount lands. It is vital to have good process control and stencil design. If this can be accomplished, it leads to a better and consistent result than when using a metal squeegee.
When using fine pitch, the process complexity increases. Considerable process development and control are required to achieve a consistently good paste print.
Paste-in-hole Process for Through-hole
As the industry moves to finer pitches and ball grid arrays (BGA), it still must deal with through-hole components in a mixed assembly. Solder paste printing generally is not used for soldering through-hole components, but there are circumstances when it should be considered. For example, in a mixed assembly with double-sided SMT boards (active components, such as plastic leaded chip carriers, on both sides) having very few through-hole components on the top side, it may be cost-effective to print paste for through-hole components. This process generally is referred to as the paste-in-hole process — it avoids the additional step of either hand or wave soldering (using customized fixtures to hide previously reflow soldered surface mount components). Pin-in-paste soldering, intrusive reflow soldering and reflow of through-hole (ROT) are other names for the process.
In such a mixed assembly, why should hand or wave soldering be avoided? When hand soldering is used, there is always the potential for internal damage, depending on operator skill. Special fixtures for wave soldering add to product cost and create the potential for solder bridging in previously reflow soldered surface mount components.
When using the conventional approach for soldering mixed surface mount assemblies, solder paste is printed and the surface mount components are reflow soldered, followed by a wavesoldering process for through-hole components. However, when using the paste-in-hole process, the surface mount and through-hole components both are soldered during the reflow soldering process. In the traditional wavesoldering process, the solder source for through-hole joints is the solder wave; for the paste-in-hole process, however, the source is solder paste.
The paste-in-hole process is relatively new, but some leading companies have done it for some time. When using the process, it first should be determined if through-hole components can withstand the reflow temperature without degradation. It also should be determined if the parts are moisture sensitive — if they are, they must be baked before soldering. Otherwise, they will “popcorn” or crack during reflow soldering.
If the board has wavesolderable surface mount components on the secondary side, through-hole component reflow soldering would not save any process steps. In such a case, wave instead of reflow soldering is the most commonly used practice for through-hole components.
The industry has struggled to successfully solder through-hole components by using the paste-in-hole process or a variation. The basic concept in all approaches revolves around printing the needed solder volume, which is determined by subtracting the volume occupied by the lead in-hole from the volume of the plated through-hole. This is simple enough and is understood by most. The problem is about half the paste disappears into thin air at soldering temperatures because a solder paste with 90 weight percent solder content is made of only 50 volume percent metallic solder. There also is the fine point of knowing the right ratio between the lead diameter and the hole so that solder can get into the hole by capillary action. The right amount of play between the hole and the lead is needed to achieve solder fill.
The IPC-610 acceptability criteria for through-hole solder joints is the presence of a bottom fillet and at least 75 percent fill up the through-hole along the board thickness. In most assemblies, circuit boards typically are 0.062" thick with an FR-4 laminate. Under these constraints, the major technical challenge of pin-in-paste process development is printing sufficient paste in and around the through-holes of components with a high pin density so acceptable solder joints are formed on the bottom side to meet IPC-610 requirements. Meeting the topside fillet requirement rarely is an issue in the paste-in-hole process because the paste is printed from the top.
The minimum gap between lead and hole determines the solder paste volume needed to meet the fillet requirement. This minimum gap is defined as maximum pin dimension minus minimum hole diameter. The smaller the minimum gap, the less solder volume is necessary to fill the through-hole, but it is more difficult to insert the component into the board.
When using fine-pitch, multi-row through-hole components, variable stencil aperture width and length may be necessary to achieve acceptable solder joints. However, fillet sizes of various solder joints in the same part would be slightly different.
To achieve the desired solder fillet volume, paste also can be printed on the top and bottom side of the board. A recent development is the use of printers with built-in squeegees that apply paste to the board by direct pressure. In this method, traditional squeegees are not used. This solder paste printing method is known to fill through-holes completely with solder paste.
The key in through-hole printing, as noted earlier, is providing sufficient solder paste volume. There are various approaches to accomplish this, the most common and desirable of which is to overprint. However, this requires that the process be planned at the design stage and sufficient interpackage spacing be allowed. If this is not done, it is impossible to overprint because other component pads will be in the way. But even if sufficient interpackage spacing is allowed, it still may be difficult to print sufficient paste if there are multiple rows of pins, such as with a fine-pitch through-hole connector.
For cases where it is difficult to apply sufficient solder paste on one side, paste can be printed on the other side, as well. Another approach is to use a step stencil that can be either stepped up or down to accommodate the varying needs of through-hole and fine-pitch components on the same board.
The stepped-up stencil is thicker (about 0.012") in a small area for through-hole parts than the rest of the stencil (0.006"). Stepped-down stencils generally are used where most of the board has standard 0.050" pitch surface mount components along with some fine-pitch components.
No matter which approach is used, the key is to apply sufficient solder paste volume.
SMT
This column is adapted from Chapter 9 of Ray Prasad’s textbook, Surface Mount Technology: Principles and Practice.
RAY P. PRASAD is an SMT Editorial Advisory Board member and author of the text book Surface Mount Technology: Principles and Practice. He is also founder of the Ray Prasad Consultancy Group which specializes in helping companies establish strong internal SMT infrastructure. Contact him at his web site: www.rayprasad.com.
In last month’s column (“Solder Paste Printing,” September 2000 SMT, p. 28-33), I discussed the basic process of solder paste printing, stencil types and design. In this column, I will apply those principles to fine-pitch and through-hole component paste printing on a mixed-assembly board.
Fine-pitch Paste Printing
When printing for fine pitch, it is important to control the smoothness and the dimensions of the stencil apertures, meaning laser-cut stencils should be considered. Fine pitch also requires different solder paste.
Solder paste print quality is very important because it accounts for numerous printed circuit assembly (PCA) defects. When using fine pitch, the problem is compounded, leading to bridging between adjacent leads.
Bridging is not the only common defect in fine-pitch printing. Inadequate paste deposition leads to insufficient solder or complete opens. In most companies, fine-pitch printing accounts for about half of all defects.
To avoid printing problems, some use dual?step stencils (0.005 to 0.006" for fine-pitch and 0.007 to 0.008" for other components). The stencil material, generally stainless steel, is etched down to a low thickness where the stencil aligns with fine-pitch component pads. Step stencils require a rubber squeegee to force the paste through the stencil holes. This is a good method for depositing the correct paste amount at specific locations (0.005 to 0.006" paste height for fine-pitch and 0.007 to 0.008" paste height for standard surface mount components).
A more recent method uses a metal squeegee and deposits the same paste thickness for both fine-pitch and other components. However, it is possible to deposit too much paste on the fine-pitch lands or too little paste on the standard surface mount lands. It is vital to have good process control and stencil design. If this can be accomplished, it leads to a better and consistent result than when using a metal squeegee.
When using fine pitch, the process complexity increases. Considerable process development and control are required to achieve a consistently good paste print.
Paste-in-hole Process for Through-hole
As the industry moves to finer pitches and ball grid arrays (BGA), it still must deal with through-hole components in a mixed assembly. Solder paste printing generally is not used for soldering through-hole components, but there are circumstances when it should be considered. For example, in a mixed assembly with double-sided SMT boards (active components, such as plastic leaded chip carriers, on both sides) having very few through-hole components on the top side, it may be cost-effective to print paste for through-hole components. This process generally is referred to as the paste-in-hole process — it avoids the additional step of either hand or wave soldering (using customized fixtures to hide previously reflow soldered surface mount components). Pin-in-paste soldering, intrusive reflow soldering and reflow of through-hole (ROT) are other names for the process.
In such a mixed assembly, why should hand or wave soldering be avoided? When hand soldering is used, there is always the potential for internal damage, depending on operator skill. Special fixtures for wave soldering add to product cost and create the potential for solder bridging in previously reflow soldered surface mount components.
When using the conventional approach for soldering mixed surface mount assemblies, solder paste is printed and the surface mount components are reflow soldered, followed by a wavesoldering process for through-hole components. However, when using the paste-in-hole process, the surface mount and through-hole components both are soldered during the reflow soldering process. In the traditional wavesoldering process, the solder source for through-hole joints is the solder wave; for the paste-in-hole process, however, the source is solder paste.
The paste-in-hole process is relatively new, but some leading companies have done it for some time. When using the process, it first should be determined if through-hole components can withstand the reflow temperature without degradation. It also should be determined if the parts are moisture sensitive — if they are, they must be baked before soldering. Otherwise, they will “popcorn” or crack during reflow soldering.
If the board has wavesolderable surface mount components on the secondary side, through-hole component reflow soldering would not save any process steps. In such a case, wave instead of reflow soldering is the most commonly used practice for through-hole components.
The industry has struggled to successfully solder through-hole components by using the paste-in-hole process or a variation. The basic concept in all approaches revolves around printing the needed solder volume, which is determined by subtracting the volume occupied by the lead in-hole from the volume of the plated through-hole. This is simple enough and is understood by most. The problem is about half the paste disappears into thin air at soldering temperatures because a solder paste with 90 weight percent solder content is made of only 50 volume percent metallic solder. There also is the fine point of knowing the right ratio between the lead diameter and the hole so that solder can get into the hole by capillary action. The right amount of play between the hole and the lead is needed to achieve solder fill.
The IPC-610 acceptability criteria for through-hole solder joints is the presence of a bottom fillet and at least 75 percent fill up the through-hole along the board thickness. In most assemblies, circuit boards typically are 0.062" thick with an FR-4 laminate. Under these constraints, the major technical challenge of pin-in-paste process development is printing sufficient paste in and around the through-holes of components with a high pin density so acceptable solder joints are formed on the bottom side to meet IPC-610 requirements. Meeting the topside fillet requirement rarely is an issue in the paste-in-hole process because the paste is printed from the top.
The minimum gap between lead and hole determines the solder paste volume needed to meet the fillet requirement. This minimum gap is defined as maximum pin dimension minus minimum hole diameter. The smaller the minimum gap, the less solder volume is necessary to fill the through-hole, but it is more difficult to insert the component into the board.
When using fine-pitch, multi-row through-hole components, variable stencil aperture width and length may be necessary to achieve acceptable solder joints. However, fillet sizes of various solder joints in the same part would be slightly different.
To achieve the desired solder fillet volume, paste also can be printed on the top and bottom side of the board. A recent development is the use of printers with built-in squeegees that apply paste to the board by direct pressure. In this method, traditional squeegees are not used. This solder paste printing method is known to fill through-holes completely with solder paste.
The key in through-hole printing, as noted earlier, is providing sufficient solder paste volume. There are various approaches to accomplish this, the most common and desirable of which is to overprint. However, this requires that the process be planned at the design stage and sufficient interpackage spacing be allowed. If this is not done, it is impossible to overprint because other component pads will be in the way. But even if sufficient interpackage spacing is allowed, it still may be difficult to print sufficient paste if there are multiple rows of pins, such as with a fine-pitch through-hole connector.
For cases where it is difficult to apply sufficient solder paste on one side, paste can be printed on the other side, as well. Another approach is to use a step stencil that can be either stepped up or down to accommodate the varying needs of through-hole and fine-pitch components on the same board.
The stepped-up stencil is thicker (about 0.012") in a small area for through-hole parts than the rest of the stencil (0.006"). Stepped-down stencils generally are used where most of the board has standard 0.050" pitch surface mount components along with some fine-pitch components.
No matter which approach is used, the key is to apply sufficient solder paste volume.
SMT
This column is adapted from Chapter 9 of Ray Prasad’s textbook, Surface Mount Technology: Principles and Practice.
RAY P. PRASAD is an SMT Editorial Advisory Board member and author of the text book Surface Mount Technology: Principles and Practice. He is also founder of the Ray Prasad Consultancy Group which specializes in helping companies establish strong internal SMT infrastructure. Contact him at his web site: www.rayprasad.com.
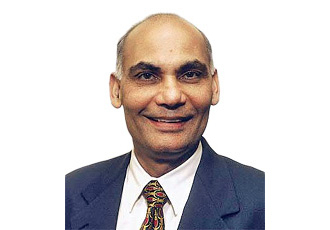
Registration is Open for SMT Course
Ray Prasad will be teaching his flagship SMT course: