SMT Solder Paste Printing for SMT Part 1
Part 1 of a 2-part series.
In surface mount assembly reflow soldering, solder paste is used for the connection between surface mount component leads or terminations and the lands. There are many variables, such as paste, screen printer, paste application method and printing process. In printing solder paste, the substrate is placed on the work holder mechanically or by vacuum, and aligned with tooling pins or vision. Either a screen or stencil is used to apply solder paste. In this column, I will focus on some key paste printing issues, such as stencil design and printing processes; in next month’s column, I will discuss printing processes for fine-pitch and through-hole components in a mixed surface mount assembly.
Printing Process and Equipment
In the solder paste printing process, the printer is crucial for achieving desired print quality. Screen printers available today fall into two main categories: laboratory and production. Each category has further subdivisions because companies expect different performance levels from laboratory and production printers. For example, a laboratory application that is R&D for one company could be prototype or production for another. Moreover, production requirements can vary widely depending on volume. Because a clear?cut equipment classification is not possible, the best thing to do is to select a screen printer to match the desired application.
In manual or semiautomatic printers, solder paste is placed manually on the stencil/screen with the print squeegee at one end of the stencil. In automatic printers, paste is dispensed automatically. During the printing process, the print squeegee presses down on the stencil to the extent that the stencil bottom touches the top board surface. Solder paste is printed on the lands through the openings in the stencil/screen when the squeegee traverses the entire image area length etched in the metal mask.
After the paste has been deposited, the screen peels away or snaps off immediately behind the squeegee and returns to its original position. This gap or snap?off distance is a function of the equipment design and is about 0.020 to 0.040". Snap?off distance and squeegee pressures are two important equipment?dependent variables for good quality printing.
If there is no snap?off, the operation is called on?contact printing. This is used when an all?metal stencil or squeegee blade is used. If there is a snap?off, the process is called off?contact printing. Off?contact printing is used with flexible metal masks and screens.
Squeegee Types
Squeegee wear, pressure and hardness determine print quality and should be monitored carefully. For acceptable print quality, squeegee edges should be sharp and straight. A low squeegee pressure results in skips and ragged edges, while a high squeegee pressure or a soft squeegee will cause smeared prints and may even damage the squeegee and stencil or screen. Excessive pressure also tends to scoop solder paste from wide apertures, causing insufficient solder fillets.
Two squeegee types are common: rubber or polyurethane squeegees and metal squeegees. When using rubber squeegees, 70 to 90 durometer hardness squeegees are used. When applying excessive pressure, paste bleeding underneath the stencil may cause bridging and will require frequent underside wiping. To prevent underside bleeding, the pad opening must provide a gasketing effect while printing. This is dependent on the roughness of the stencil aperture walls.
Metal squeegees also are commonly used. Their popularity has grown with the use of finer pitch components. They are made from stainless steel or brass in a flat blade configuration, and are used at a 30° to 45° print angle. Some squeegees are coated with lubricating material. Because lower pressure is used, they do not scoop paste from apertures, and because they are metallic, they do not wear easily like rubber squeegees and hence do not need to be sharpened. They cost significantly more than rubber squeegees, and can cause stencil wear.
Using different squeegee types has ramifications in printed circuit assemblies (PCA) with both standard and fine-pitch components. The solder paste volume requirement is very different for each component type. Fine-pitch components require much less solder volume than standard surface mount components. Pad area and thickness control solder paste volume.
Some engineers use dual-thickness stencil to apply the appropriate paste amount at fine-pitch and standard surface mount pads. This is the conventional approach and requires a rubber squeegee to force paste through the stencil holes. Other engineers take a different approach — they use a more expensive metal squeegee that does not require frequent sharpening. It is easier to prevent variation in paste volume deposition with a metal squeegee, but this approach requires a modified stencil aperture design to prevent excess paste deposition on fine-pitch pads. The approach has become more popular in the industry, but rubber squeegees with dual-thickness printing have not vanished.
Stencil Types
Important print quality variables include accuracy and smoothness of the stencil aperture sidewalls. Maintaining a proper aspect ratio between stencil width and thickness is important. The recommended aspect ratio (aperture width divided by stencil thickness) is 1.5. This is important for preventing stencil clogging. Generally, solder paste remains in the opening if the aspect ratio is less than 1.5. In addition to aspect ratio, it also is good to have an area ratio (area of pad divided by area of aperture walls) of greater than 0.66, as recommended by IPC-7525, Stencil Design Guidelines. (This document can serve as a good starting point for stencil design.)
The process by which the aperture is made controls both the smoothness and accuracy of aperture walls. There are three common processes for making stencils: chemical etching, laser cutting and the additive process.
Chemically Etched Stencils
Metal mask and flexible metal mask stencils are etched by chemical milling from both sides using two positive images. During this process, etching proceeds not only in the desired vertical direction but also laterally. This is called undercutting — the openings are larger than desired, causing extra solder deposit. Because 50/50 etching proceeds from both sides, it results in almost a straight wall tapering to a slight hourglass shape in the center.
Because electroetched stencil walls may not be smooth, electropolishing, a microetching process, is one method for achieving a smooth wall. Another way to achieve smoother side walls in the aperture is nickel plating. A polished or smooth surface is good for paste release but may cause the paste to skip across the stencil surface rather than roll in front of the squeegee. This problem can be avoided by selectively polishing the aperture walls without polishing the stencil surface. Nickel plating further improves smoothness and printing performance. However, it does reduce aperture opening and requires artwork adjustment.
Laser-cut Stencils
Laser cutting also is a subtractive process, but it does not have the undercutting problem. The stencil is produced directly from the Gerber data, so aperture accuracy is improved. The data can be adjusted to change dimensions as necessary. Better process control also improves aperture accuracy. Another benefit of laser-cut stencils is that the walls can be tapered. Chemically etched stencils also can be tapered if they are etched only from one side, but the aperture size may be too large. A tapered aperture with an opening slightly larger on the board side than on the squeegee side (0.001 to 0.002" to produce an angle of about 2°) is desired for easier paste release.
Laser cut is capable of producing aperture widths as small as 0.004" with an accuracy of 0.0005", so it is very suitable for ultra-fine-pitch component printing. Laser-cut stencils also produce ragged edges because the vaporized metal is transformed into metal slag during the cutting process. This can cause paste clogging. Smoother walls can be produced by microetching. Laser-cut stencils cannot make stepped multilevel stencils without prechemical etching of the areas that need to be thinner. The laser cuts each aperture individually, so stencil cost depends upon the number of apertures to be cut.
Electroformed Stencils
The third process for making stencils is the additive process, most commonly called electroforming. In this process, nickel is deposited on a copper mandrel to build the aperture. A photosensitive dry film is laminated on the copper foil (about 0.25" thick). The film is polymerized by ultraviolet (UV) light through a photomask of the stencil pattern. After developing, a negative image is created on the mandrel where only the stencil apertures remain covered by the photoresist. The stencil is then grown by nickel plating around the photoresist. After achieving the desired stencil thickness, the photoresist is removed from the apertures. The electroformed nickel foil is separated from the mandrel by flexing — a key process step. Now the foil is ready for framing as in other stencil making processes.
Electroforming step stencils can be done at added cost. Because of the close tolerances possible, electroformed stencils provide a good gasket effect, which minimizes under-stencil paste seepage. This means that the frequency of underside stencil wiping is reduced drastically, which reduces potential bridges.
Conclusion
Chemical etching and laser cutting are subtractive processes for making stencils. The chemical-etch process is the oldest and most widely used. Laser cut is a relative newcomer, while electroformed stencils are the latest rage.
To achieve good printing results, a combination of the right paste material (viscosity, metal content, largest powder size and lowest flux activity possible), the right tools (printer, stencil and squeegee blade) and the right process (good registration, clean sweep) are necessary.
Even the best pastes, equipment and application methods do not sufficiently ensure acceptable results. The user must control process and equipment variables to achieve good print quality. This is even more critical in fine-pitch and through-hole printing — the subject of my next column.
SMT
This column is adapted from Chapter 9 of Ray Prasad’s textbook, Surface Mount Technology: Principles and Practice.
RAY P. PRASAD is an SMT Editorial Advisory Board member and author of the text book Surface Mount Technology: Principles and Practice. He is also founder of the Ray Prasad Consultancy Group which specializes in helping companies establish strong internal SMT infrastructure. Contact him at his website www.rayprasad.com.
In surface mount assembly reflow soldering, solder paste is used for the connection between surface mount component leads or terminations and the lands. There are many variables, such as paste, screen printer, paste application method and printing process. In printing solder paste, the substrate is placed on the work holder mechanically or by vacuum, and aligned with tooling pins or vision. Either a screen or stencil is used to apply solder paste. In this column, I will focus on some key paste printing issues, such as stencil design and printing processes; in next month’s column, I will discuss printing processes for fine-pitch and through-hole components in a mixed surface mount assembly.
Printing Process and Equipment
In the solder paste printing process, the printer is crucial for achieving desired print quality. Screen printers available today fall into two main categories: laboratory and production. Each category has further subdivisions because companies expect different performance levels from laboratory and production printers. For example, a laboratory application that is R&D for one company could be prototype or production for another. Moreover, production requirements can vary widely depending on volume. Because a clear?cut equipment classification is not possible, the best thing to do is to select a screen printer to match the desired application.
In manual or semiautomatic printers, solder paste is placed manually on the stencil/screen with the print squeegee at one end of the stencil. In automatic printers, paste is dispensed automatically. During the printing process, the print squeegee presses down on the stencil to the extent that the stencil bottom touches the top board surface. Solder paste is printed on the lands through the openings in the stencil/screen when the squeegee traverses the entire image area length etched in the metal mask.
After the paste has been deposited, the screen peels away or snaps off immediately behind the squeegee and returns to its original position. This gap or snap?off distance is a function of the equipment design and is about 0.020 to 0.040". Snap?off distance and squeegee pressures are two important equipment?dependent variables for good quality printing.
If there is no snap?off, the operation is called on?contact printing. This is used when an all?metal stencil or squeegee blade is used. If there is a snap?off, the process is called off?contact printing. Off?contact printing is used with flexible metal masks and screens.
Squeegee Types
Squeegee wear, pressure and hardness determine print quality and should be monitored carefully. For acceptable print quality, squeegee edges should be sharp and straight. A low squeegee pressure results in skips and ragged edges, while a high squeegee pressure or a soft squeegee will cause smeared prints and may even damage the squeegee and stencil or screen. Excessive pressure also tends to scoop solder paste from wide apertures, causing insufficient solder fillets.
Two squeegee types are common: rubber or polyurethane squeegees and metal squeegees. When using rubber squeegees, 70 to 90 durometer hardness squeegees are used. When applying excessive pressure, paste bleeding underneath the stencil may cause bridging and will require frequent underside wiping. To prevent underside bleeding, the pad opening must provide a gasketing effect while printing. This is dependent on the roughness of the stencil aperture walls.
Metal squeegees also are commonly used. Their popularity has grown with the use of finer pitch components. They are made from stainless steel or brass in a flat blade configuration, and are used at a 30° to 45° print angle. Some squeegees are coated with lubricating material. Because lower pressure is used, they do not scoop paste from apertures, and because they are metallic, they do not wear easily like rubber squeegees and hence do not need to be sharpened. They cost significantly more than rubber squeegees, and can cause stencil wear.
Using different squeegee types has ramifications in printed circuit assemblies (PCA) with both standard and fine-pitch components. The solder paste volume requirement is very different for each component type. Fine-pitch components require much less solder volume than standard surface mount components. Pad area and thickness control solder paste volume.
Some engineers use dual-thickness stencil to apply the appropriate paste amount at fine-pitch and standard surface mount pads. This is the conventional approach and requires a rubber squeegee to force paste through the stencil holes. Other engineers take a different approach — they use a more expensive metal squeegee that does not require frequent sharpening. It is easier to prevent variation in paste volume deposition with a metal squeegee, but this approach requires a modified stencil aperture design to prevent excess paste deposition on fine-pitch pads. The approach has become more popular in the industry, but rubber squeegees with dual-thickness printing have not vanished.
Stencil Types
Important print quality variables include accuracy and smoothness of the stencil aperture sidewalls. Maintaining a proper aspect ratio between stencil width and thickness is important. The recommended aspect ratio (aperture width divided by stencil thickness) is 1.5. This is important for preventing stencil clogging. Generally, solder paste remains in the opening if the aspect ratio is less than 1.5. In addition to aspect ratio, it also is good to have an area ratio (area of pad divided by area of aperture walls) of greater than 0.66, as recommended by IPC-7525, Stencil Design Guidelines. (This document can serve as a good starting point for stencil design.)
The process by which the aperture is made controls both the smoothness and accuracy of aperture walls. There are three common processes for making stencils: chemical etching, laser cutting and the additive process.
Chemically Etched Stencils
Metal mask and flexible metal mask stencils are etched by chemical milling from both sides using two positive images. During this process, etching proceeds not only in the desired vertical direction but also laterally. This is called undercutting — the openings are larger than desired, causing extra solder deposit. Because 50/50 etching proceeds from both sides, it results in almost a straight wall tapering to a slight hourglass shape in the center.
Because electroetched stencil walls may not be smooth, electropolishing, a microetching process, is one method for achieving a smooth wall. Another way to achieve smoother side walls in the aperture is nickel plating. A polished or smooth surface is good for paste release but may cause the paste to skip across the stencil surface rather than roll in front of the squeegee. This problem can be avoided by selectively polishing the aperture walls without polishing the stencil surface. Nickel plating further improves smoothness and printing performance. However, it does reduce aperture opening and requires artwork adjustment.
Laser-cut Stencils
Laser cutting also is a subtractive process, but it does not have the undercutting problem. The stencil is produced directly from the Gerber data, so aperture accuracy is improved. The data can be adjusted to change dimensions as necessary. Better process control also improves aperture accuracy. Another benefit of laser-cut stencils is that the walls can be tapered. Chemically etched stencils also can be tapered if they are etched only from one side, but the aperture size may be too large. A tapered aperture with an opening slightly larger on the board side than on the squeegee side (0.001 to 0.002" to produce an angle of about 2°) is desired for easier paste release.
Laser cut is capable of producing aperture widths as small as 0.004" with an accuracy of 0.0005", so it is very suitable for ultra-fine-pitch component printing. Laser-cut stencils also produce ragged edges because the vaporized metal is transformed into metal slag during the cutting process. This can cause paste clogging. Smoother walls can be produced by microetching. Laser-cut stencils cannot make stepped multilevel stencils without prechemical etching of the areas that need to be thinner. The laser cuts each aperture individually, so stencil cost depends upon the number of apertures to be cut.
Electroformed Stencils
The third process for making stencils is the additive process, most commonly called electroforming. In this process, nickel is deposited on a copper mandrel to build the aperture. A photosensitive dry film is laminated on the copper foil (about 0.25" thick). The film is polymerized by ultraviolet (UV) light through a photomask of the stencil pattern. After developing, a negative image is created on the mandrel where only the stencil apertures remain covered by the photoresist. The stencil is then grown by nickel plating around the photoresist. After achieving the desired stencil thickness, the photoresist is removed from the apertures. The electroformed nickel foil is separated from the mandrel by flexing — a key process step. Now the foil is ready for framing as in other stencil making processes.
Electroforming step stencils can be done at added cost. Because of the close tolerances possible, electroformed stencils provide a good gasket effect, which minimizes under-stencil paste seepage. This means that the frequency of underside stencil wiping is reduced drastically, which reduces potential bridges.
Conclusion
Chemical etching and laser cutting are subtractive processes for making stencils. The chemical-etch process is the oldest and most widely used. Laser cut is a relative newcomer, while electroformed stencils are the latest rage.
To achieve good printing results, a combination of the right paste material (viscosity, metal content, largest powder size and lowest flux activity possible), the right tools (printer, stencil and squeegee blade) and the right process (good registration, clean sweep) are necessary.
Even the best pastes, equipment and application methods do not sufficiently ensure acceptable results. The user must control process and equipment variables to achieve good print quality. This is even more critical in fine-pitch and through-hole printing — the subject of my next column.
SMT
This column is adapted from Chapter 9 of Ray Prasad’s textbook, Surface Mount Technology: Principles and Practice.
RAY P. PRASAD is an SMT Editorial Advisory Board member and author of the text book Surface Mount Technology: Principles and Practice. He is also founder of the Ray Prasad Consultancy Group which specializes in helping companies establish strong internal SMT infrastructure. Contact him at his website www.rayprasad.com.
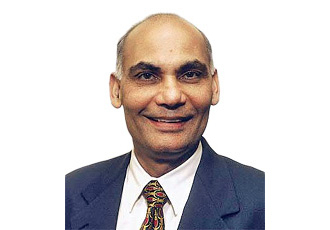
Registration is Open for SMT Course
Ray Prasad will be teaching his flagship SMT course: